AQL Standard (Single sampling plan for normal inspection)
QCINASIA uses well-proven and widely adopted international standard ISO2859-1 (equivalent of ANSI/ASQC Z1.4-2008, BS 6001, ABC-105, NFX06 –022, NFX 06-022, DIN 40.080, UNI 48.42) Single Sampling Plan. General Inspection Level Normal II is usually applied to determine the inspection sample size for aesthetic and functional check. Special Inspection Level will be applied for safety, reliability, performance or other special test if whereas applicable.
AQL Table
Table A:
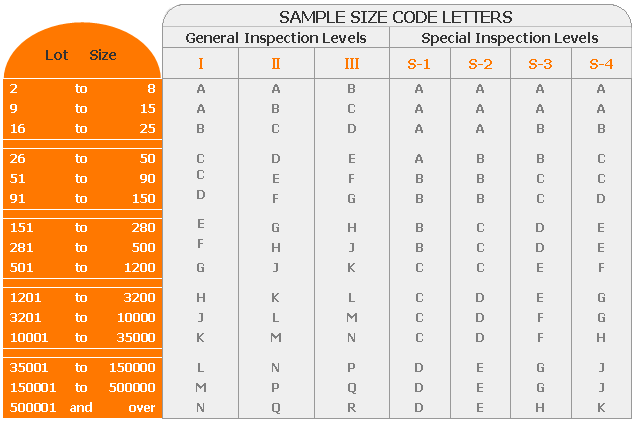
Table B:
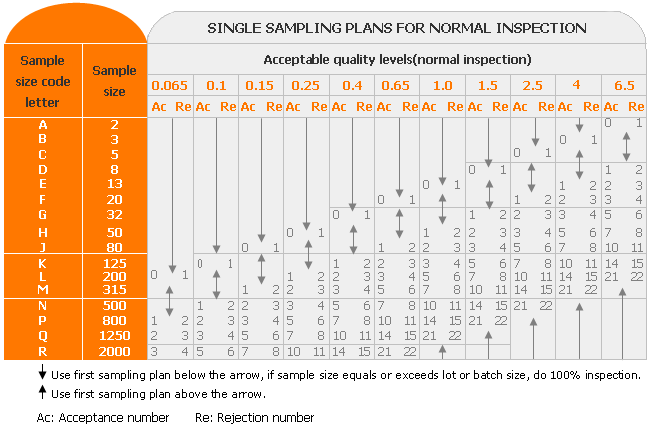
The inspection level designates the relative amount of inspection. Three inspection levels, I, II and III, are given in Table A for general use. Unless otherwise specified, level II shall be used. Level I may be used when less discrimination is needed or level III when greater discrimination is required. Four additional special levels, S-1, S-2, S-3 and S-4 are also given in Table A and may be used where relatively small sample sizes are necessary (for example, for some destructive test or time-consuming test) and larger sampling risks can be tolerated.
Sample sizes are designated by sample size code letters and the corresponding AQL level. Table A shall be used to find the applicable code letter for the particular lot size, Table B shall be used to find the sample size based on code letter and the prescribed AQL level.
As default, QCINASIA uses general inspection level II, Acceptable Quality Level (AQL) Not allowed / 2.5 / 4.0 of Critical, Major, Minor defect.
For example, there're 6,000 units to be inspected. As per single sampling level II, AQL: Not allowed / 2.5 / 4.0 of Critical / Major / Minor:
According to table A, from quantity 3201 to 10000, the corresponding sample size code letter is "L", therefore in table B, “L” is corresponding to sample size "200". So the maximum allowed number of defective unit is as follow:
Critical Defect 0; Major Defect 10; Minor Defect: 14.
In other words, if the number of critical defective units is more than 0, or major defective units is more than 10, or minor defective units is more than 14, the lot has to be rejected.
Defects Classification Criteria
Defects detected during inspection are classified within 3 categories -"Critical", " Major ", " Minor "and the normal definitions are:
Critical: Defects which could result in hazardous or unsafe conditions for individuals using or maintaining the product as well as defects contravening legal regulations.
Major: Functional defects reducing the usability or solidity of the product as well as obvious visual defects reducing the sales value of the product.
Minor: Defects that are unlikely to reduce the use of the product, but nevertheless may influence the sale.
For random inspection, the following rules are applied:
If the same sample has several defects, only the most serious defect is counted.
In the case of critical defects, the entire shipment must be rejected as a matter of principle and clients consulted for a decision.